Clever way of saving water brings reward
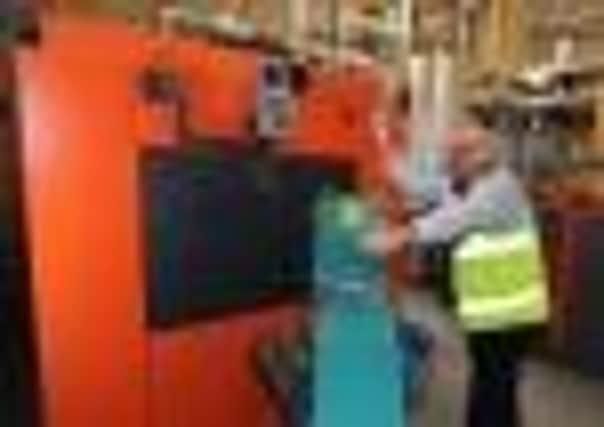

Ilkley-based NG Bailey, one of the UK’s leading independent engineering, IT and facilities services businesses, with a turnover of £450m, has devised and developed a pioneering filtering system in an attempt to reduce water usage on construction sites.
The company believes it could save up to 20m litres of water a year on NG Bailey sites alone – the equivalent of eight Olympic sized swimming pools. The fact that its idea can be broadly replicated attracted praise from the judges.
Advertisement
Hide AdAdvertisement
Hide AdIn 2010, NG Bailey launched its Target2012 sustainability campaign, which set out four main challenges for the company to achieve by the end of 2012. One was reducing water usage by 20 per cent.


In particular, the firm wanted to address the problem of excessive water usage during the commissioning of heating and cooling systems. The process can use more than eight times the system volume, as it is flushed to test it and rid it of any impurities.
Initially, the NG Bailey team developed the equivalent of a construction site “kidney dialysis” machine; a trailer-mountable filtration system that could be transported from site to site.
The heating system would be filled with water as normal, and, instead of being flushed away each time, the same water could be filtered and re-used. However, this was deemed impractical and costly in terms of transportation. It didn’t chime with company’s aims of reducing vehicle movements. So the team then looked to the actual filtration application.
Advertisement
Hide AdAdvertisement
Hide AdThey identified that through a combination of specifying pipework systems which use “press connection” systems, which avoid the need for soldering or welding, and the introduction of an inline filtering system, commissioning water waste could be all but eradicated.
In January this year, the team demonstrated its findings at one of NG Bailey’s construction projects in South Yorkshire. This exercise saw 32,000 litres of water being pumped into the chilled beam units. A conventional commissioning exercise would have resulted in a total of 256,000 litres being used, and, ultimately, wasted.
The pilot process produced just 600 litres of water waste. In addition, the water used in the flushing process was then left in the system, saving the end client water costs throughout the ongoing maintenance of the system during its life.
With a target of reducing water usage by 20 per cent, this process will save almost 100 per cent, according to NG Bailey. Now successfully trialled in the Yorkshire region, the next stage is to roll this out as a standard procedure on all applicable future projects.
Cal Bailey, a director, said sustainability is “a business imperative and an imperative to everyone who lives in this world”.