How Yorkshire manufacturers are rising to the biggest challenge in living memory
But now as companies face up having to adapt to the immense challenges presented during the coronavirus pandemic, the region’s entrepreneurs are tackling the biggest challenges the manufacturing sector has faced in living memory.
When Boris Johnson issued an unprecedented peacetime call to arms last month asking businesses to transform their current production lines to help produce 30,000 ventilators as part of a "national effort" to tackle the Coronavirus, a huge number of Yorkshire businesses answered the call.
Advertisement
Hide AdAdvertisement
Hide AdAerospace company Produmax, which usually makes flight control components, has implemented split shifts around the clock to produce vital ventilator parts at speed from their Baildon site in West Yorkshire.
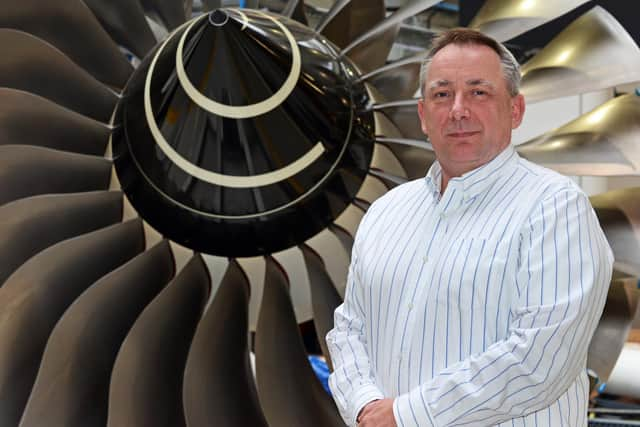

The firm’s 90 staff are manufacturing 10 different types of components that will be assembled on the new NHS ventilators.
Over the next few weeks it will make over 60,000 brass, steel and plastic components on its lathes, which will then make their way onto the air flow control units of Penlon and Smiths Medical ventilators.
Speaking to The Yorkshire Post, financial director Mandy Ridyard said: “We’re not in this to make a profit. “We’re producing the components at cost because it’s the right thing to do.
"Our team is proud to be part of the national effort.”
Advertisement
Hide AdAdvertisement
Hide Ad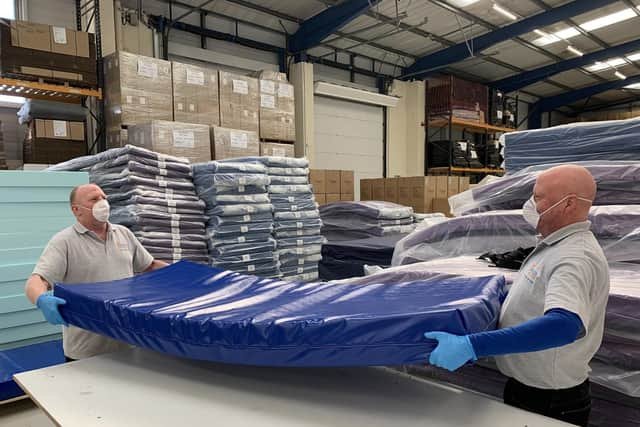

It is also programming futuristic headsets - initially designed for use in gaming - to enable skilled aerospace and automotive production line operatives to rapidly switch to the manufacture of 10,000 life-saving medical ventilators.
It said the augmented reality equipment is critical to the success of the industrial consortium - Ventilator Challenge UK - which includes manufacturing heavyweights McLaren and Rolls Royce, has come together to accelerate production before the Covid-19 pandemic reaches its peak.
“What we are seeing in South Yorkshire...is part of a truly nationwide and global response to the Covid-19 pandemic,” said the AMRC’s head of digital, Professor Rab Scott.
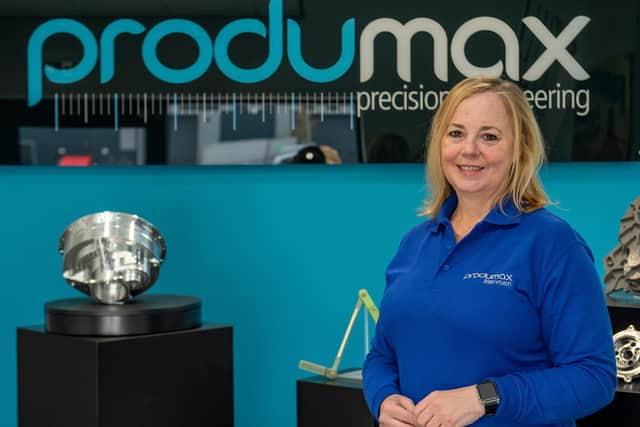

Within hours of the Prime Minister laying down his ventilator challenge, the AMRC and Nuclear AMRC were taking scores of requests for assistance, not just for ventilators, but also for medical equipment such as face masks and swabs and vials for Covid-19 test kits.
Advertisement
Hide AdAdvertisement
Hide AdAt the same time as Prof Scott was putting the finishing touches to the HoloLens deployment, the AMRC’s Machining Group, was scrambling staff working from home back to the shop floor to make critical components to scale-up its tried-and-tested ventilators, already used in hospitals and ambulances.
Over in North Yorkshire, Mowden Controls is manufacturing the electronics for oxygen monitors used in a breathing aid that can help keep coronavirus patients out of intensive care
The Continuous Positive Airway Pressure (CPAP) devices, which are being made by Mercedes Formula One and University College London, are the step before ventilation.
The Northallerton-based company, which employs 47 people and usually makes electronics for medical, cryogenics, oil and gas, and aerospace sectors among others, has delivered an initial small batch. It is now working as fast as possible over Easter on an order to deliver 10,000 electronics assemblies.
Advertisement
Hide AdAdvertisement
Hide AdBut it’s not only ventilators and breathing aids that manufacturers are producing .
Yorkshire firms are also making hospital mattresses, faceguards and face masks. Mattress manufacturers Herida Healthcare and GNG Group are increasing production to supply the NHS.
Leeds-based Herida is to supply 12,000 mattresses to the new NHS super hospitals currently being set up across the country, building on the 2,000 mattresses the company has already supplied to the NHS Nightingale hospital in London.
Wakefield-based GNG Group, a specialist foam manufacturer of sports, healthcare, safety and mattress products, has paused production in all other divisions in order to enable a 90-strong team to focus on production of healthcare mattresses destined for the NHS Nightingale project and several key NHS suppliers manufacturing hospital beds.
Advertisement
Hide AdAdvertisement
Hide AdManaging director Phil Whittell said it was the biggest challenge the company had faced in its 45-year history: “Incredibly, we’ve received the equivalent of six months of orders in the last five days and we currently have 16,000 medical mattresses shipped or on order since the crisis started,” he said.
The region’s universities are also stepping up to play their part. Huddersfield University’s 3M Buckley Innovation Centre is using 3D printing to produce 16 sets of head and chin restraints every day. The components will be fitted to shields designed to protect people staffing shops and other environments - against transmission of the virus.
Meanwhile, Hull University is leading a collaboration to produce face shields to support the NHS and other healthcare organisations in the region – with new designs and agile manufacturing techniques set to increase production capacity across the country.
The designs, which can be mass produced using laser cutting and injection moulding, will be shared nationally to enable production in other regions for the NHS and healthcare organisations.
Advertisement
Hide AdAdvertisement
Hide AdNathan Brown, senior lecturer in the department of engineering and lead on this project, said: "While it has been brilliant to see our region come together to produce face shields in line with the global initiative by 3D printing, we have established that this method is time-intensive – even with the best 3D printers available – and may not be able to generate the stocks needed by all the healthcare organisations in our region.”
So far, the collaboration has delivered approximately 500 face shields in under four days and now aims to produce more than 20,000 face shields per week. The printing industry has also risen to the coronavirus challenge.
Leeds-based Imageco, which usually produces large graphics for hospital wards, is using its cutting and sewing equipment to create face guards as well as hand sanitising stations and social distancing point of sale boards.
The company has already donated 50 protective guards to Leeds General Infirmary and 20 to a care home.
Advertisement
Hide AdAdvertisement
Hide AdNathan Swinson-Bullough, director of Imageco, said: “We sat down as a team and really thought about creative ways that would benefit others while being able to sustain our business through this crisis. I saw balancing live work with product donations as a good path to choose.
“This is the least we can do; our thoughts go out to all the staff on the frontline and the families affected by this awful crisis.”