A W Hainsworth: How an eighth-generation Yorkshire woollen mill has survived and thrived for 240 years
All of those items, and a great deal more besides, have their roots at the AW Hainsworth woollen mill in Stanningley.
The company was founded back in 1783 by enterprising 14-year-old Abimelech Hainsworth, who initially bought cloth from cottage weavers in the Farsley area and then transported to Leeds by horse and cart for sale.
Advertisement
Hide AdAdvertisement
Hide AdHe began his business with just half-a-crown but by 1800 had been successful enough to buy four acres of land in Farsley and start his own cloth production business - eventually evolving into the business that still exists today and remains in the hands of the Hainsworth family.
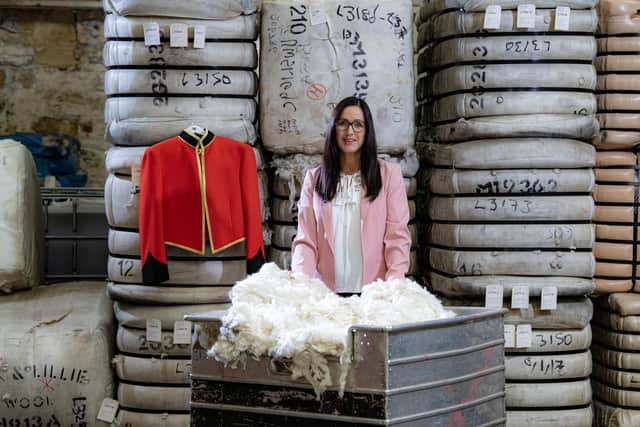

The firm is now celebrating its 240th anniversary this year with a series of special events for its 200 staff and its litany of loyal customers.
While over the decades many textile mills which once dominated their local areas have fallen by the wayside, AW Hainsworth is still going strong.
Managing director Amanda McLaren says its enduring success is in large part down to the Hainsworth family’s determination.
Advertisement
Hide AdAdvertisement
Hide Ad“The family have always had an appetite to never let the mill go, no matter what they were faced with,” she says.
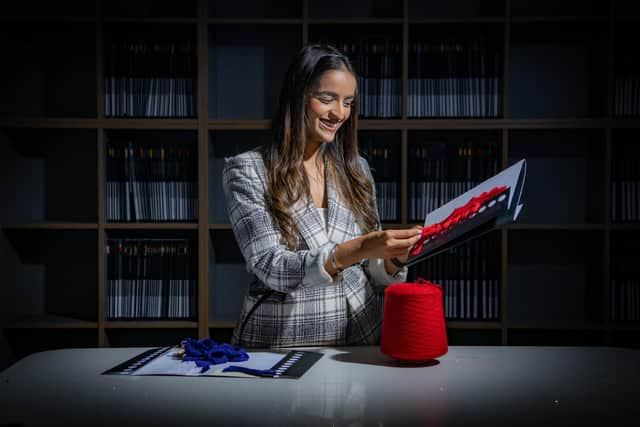

“Whether it was fire, whether it was flood, whether it was an acquisition that didn’t go so well, they had an incredible level of resilience that kept them pushing forward.
“They were championing how to look after people, how to make profit and how to constantly reinvest it.
“They did a number of acquisitions in the 1970s and 1980s where they bought up different brands and businesses that were falling by the wayside they thought would give them a wider portfolio and reduce their risk.
Advertisement
Hide AdAdvertisement
Hide Ad“If you look at our business today, we have got six very clear divisions of the business that are really different sectors. That is borne from that history and taking those risks.
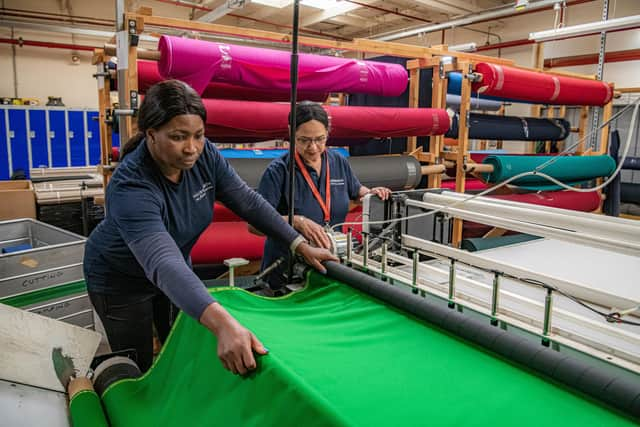

“Also they have really steered towards the heart of a woollen mill and being fully integrated; having the control over every part of the process which is quite rare. We are fully integrated from creating our own yarn, weaving our own fabrics, dyeing our fabric, finishing it and turning it into iconic cloth under one roof. That is something they have really guarded.”
AW Hainsworth’s fabrics are used in many industries - from leading fashion brands to luxury car interiors.
Appropriately for a company that is an official Royal Warrant Holder, Hainsworth fabrics were on display not just at the Coronation of King Charles but also that of his mother Queen Elizabeth II back in 1953.
Advertisement
Hide AdAdvertisement
Hide AdMcLaren explains: “It was the ceremonial uniforms - all that red fabric is made here. It goes back to the Battle of Waterloo and the phrase ‘the thin red line’ which is how the British troops were recognised. That was made here and we’ve made fabrics for World War I, for World War II.
“We’ve got many many decades of history of supplying ceremonial cloth and certainly for the Armed Forces.
“We work with garment partners who create those uniforms but the fabric comes from this mill.
“If you think about the red scarlet, it is an art to get that red exactly that colour. The match between each uniform has to be perfect and our capability of dyeing that red fabric is unique.”
Advertisement
Hide AdAdvertisement
Hide AdHainsworth’s snooker cloth was used for the British Snooker Championships when they were shown in colour on television for the first time in 1979 and continue to produce high-quality products for the sport to this day which McLaren says is particularly popular in China.
“We have a particular precision cloth and it is one most professional players in the Far East would pay to play on. The speed of the ball is improved when you play on a Hainsworth professional cloth.”
More recently, Hainsworth’s costume fabrics were used to produce the cloaks that the Death Eaters wore in West End production Harry Potter And The Cursed Child, and to dress characters in Downton Abbey, Queen Charlotte, Hamilton, Game of Thrones, and the Crown.
McLaren says the company has benefited from the rise in streaming services making their own television programmes and films.
Advertisement
Hide AdAdvertisement
Hide Ad“It is re-enactment so who better to come to than the people who supply ceremonial uniforms?
“We’ve always had a place in that market and obviously as people like Amazon and Netflix have come along and the number of series being made has increased, we have been a natural go-to as a supplier for garment manufacturers.”
McLaren joined AW Hainsworth in April 2021 after previously being MD at Halifax firm James Heal, which tests textile products.
She says the opportunity to join AW Hainsworth was one she couldn’t turn down.
Advertisement
Hide AdAdvertisement
Hide Ad“Globally most of the mills now are in the Indian subcontinent, China and Turkey where labour is cheaper. I spent a lot of time going into mills and was obviously aware of Hainsworths as a customer of James Heal’s. It was also a supplier so I’ve always had a relationship with Hainsworths from a professional perspective.
“When the Hainsworth family were reflecting post-Covid on the position of the business and the challenges they had to overcome to see it into the next 100 years, they decided to go down a non-family leader approach to set the strategy for the future and that’s when I came in. It was a bit of a hand in glove for me.
“A good third of the workforce has been here less than two years. Covid was a big disruptor for everybody and we are no different. We also lost some headcount post-Covid but there has been a very quick bounceback and we have had to rebuild that skillset.
“You can’t easily go out and find weavers so we are bringing through younger members of staff on training development programmes.”
Advertisement
Hide AdAdvertisement
Hide AdShe adds: “I see myself as a custodian because I think there’s so much heritage and history behind the brand and story that you can’t help connect with it and feel pride in it. Within days of being here I felt a sense of pride - I even felt proud of the business even at the interview stage and listening to the family about how much they care and how much it is in their blood.
“It was then about, how do I guard this and run it where it still feels like a family business but we are running in a bit more of a corporate style where profit is something we are much more specific about.
“The family wants this mill and this building to continue and therefore your strategy is built around that. It is not about being controversial or disrupting things, it is about respecting the heritage and building on that foundation.
“We’re a brand established since 1783 and we want to hold a position in the premium space; making sure what the customer gets is at or exceeds their expectations and they can rely on that for generations ahead.
Advertisement
Hide AdAdvertisement
Hide Ad“The art of what we do isn’t easy and with it comes an awful lot of expertise and know-how within the mill and we have to guard that.
“It is absolutely fantastic the business has stayed in this area and served the community around it and employed the community around it.”