Meet the young craftsmen future proofing York Minister
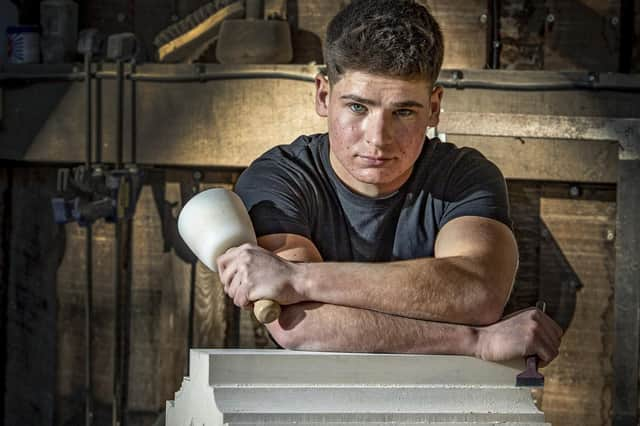

There is stone dust in the air as Charlie Gee chips at a block in the York Minster Stoneyard. That dust is in his blood too as he is the son of a stonemason. Gee has been working on this pristine slab of Tadcaster limestone for two or three weeks, using
mallets and chisels to coax the stone into shape. Other stonemasons are in full flow and there is a rhythmic quality to their chipping and bashing. The sound of stone being hit is unexpectedly musical. “Yeah, you can have a little groove to it,” Gee says, laughing.
Advertisement
Hide AdAdvertisement
Hide AdMany of his workmates wear headphones and Gee, who is 19 and halfway through his four-year apprenticeship at the stoneyard, often listens to podcasts, a nice modern touch to keeping alive an old tradition.
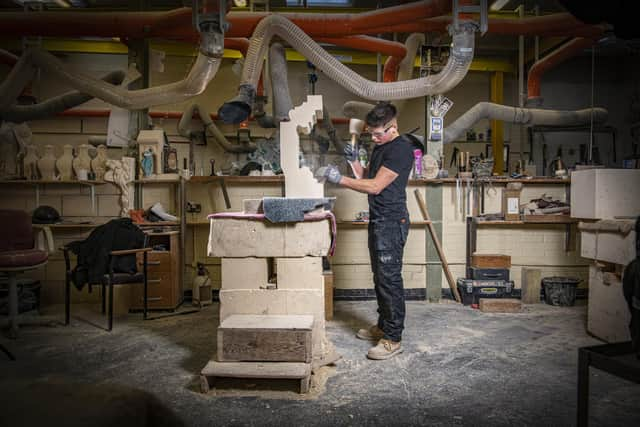

The block he is shaping is destined for the South Quire Transept on the right side of St Cuthbert’s Window.
Gee has handled stone from a young age. His father restores old buildings, and Gee was in and out of cathedrals as a child. When he was five, the family moved from Dorset to Italy, living in Anghiari, a small hill town in Tuscany, a short
drive from Florence, Siena and Assisi, an area with no shortage of fine buildings needing loving attention.
Advertisement
Hide AdAdvertisement
Hide AdIn 2012 the family moved back to Lyme Regis, where his father won the contract to conserve the Cobb, the Grade I-listed old stone harbour wall, and a young Charlie helped with that job.
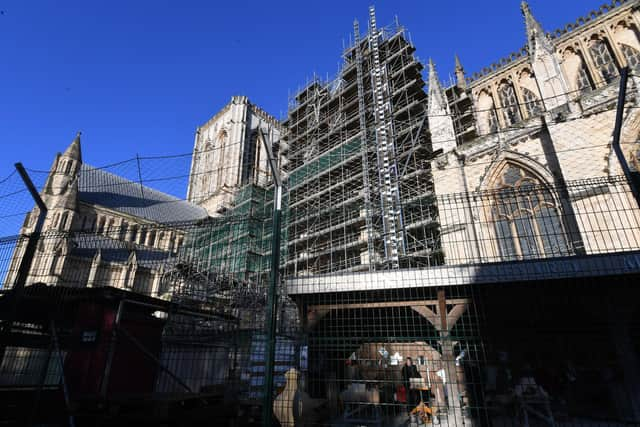

Stonemasons today work by hand, much as their medieval forebears did, although the blocks are sawn by machine before the painstaking chiselling begins. One philosophical difference is that they know what they are working on, whereas their medieval cousins laid the stones for a great edifice that they would never see completed.
“Sometimes I look up at the Minster, and as a stonemason you know how much it takes to work on each individual piece,” says Gee. “I look up and think of each individual mason who’s worked on each block that’s gone into the Minster. And it’s just incredible the amount of work there.”
After school, he went to Weymouth College, one of a few to offer stonemasonry as a subject. The college is close to where Portland stone comes from, and that prized stone is much like the block that he is shaping now.
Advertisement
Hide AdAdvertisement
Hide AdMedieval stonemasons used to carve their mark into each stone they finished. This allowed them to be paid. Each had their own “mason’s mark” and these personal indentations have been found on stones in parts of the cathedral dating to 1154.
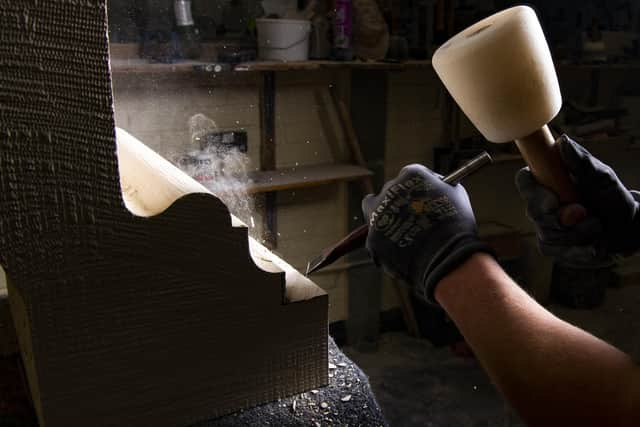

The tradition continues and Gee’s mark is formed from his initials. “I came up with that design, I just whack it in,” he says. “Whack there, whack here, it’s quite simple.”
One of the benefits of the job comes when the stones are installed. “It’s incredible when you are working up on the scaffolding and you’ve got the view of the whole of York,” Gee says.
Fixer masons usually put the stones in place, but the apprentices help. That job is saved for the summer as the lime mortar holding the stones doesn’t like the cold.
Advertisement
Hide AdAdvertisement
Hide AdHis friends at home think it’s “incredible” that Gee is working at York Minster, and his old college is proud of his progress.
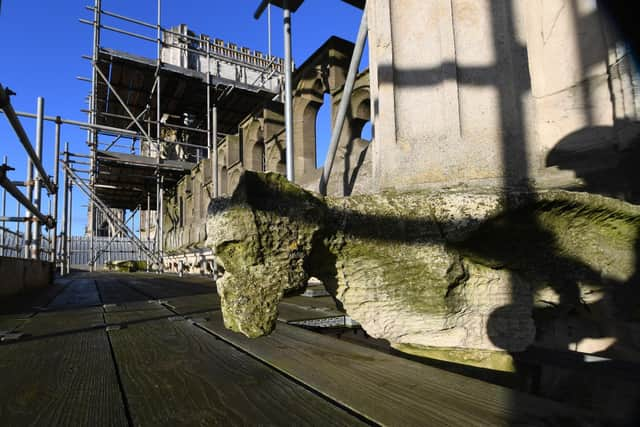

“It’s quite a privilege,” he says. “I feel really proud of the Minster, and it’s opened a lot of opportunities. I’m really enjoying working at the Minster and just completed a stone-carving project for Sky Arts and got to meet Prince Charles.” That programme is due to be screened in the next two months.
Gee says he is “constantly learning, constantly doing different things, there’s so much to the job”.
“There’s carving, there’s masonry, there’s fixing up little repairs up on the Minster. Masonry is exact geometry and exact measurements, and carving is a bit freer, a bit more artistic”.
Advertisement
Hide AdAdvertisement
Hide AdGee would “love to do a gargoyle” during his time at the Minster, a bit of rudeness or grotesquery in stone to be remembered by.
Seeing the stonemasons at work suggests that York Minster is solid and strong, a permanent edifice in stone. Yet this is far from the truth, as historic cathedrals are fragile and in need of constant attention.
One man who knows this to be so is Alex McCallion, director of works and precinct at York Minster. His office above the stoneyard affords a private view of the honeyed stone of the Minster under a cold blue sky.
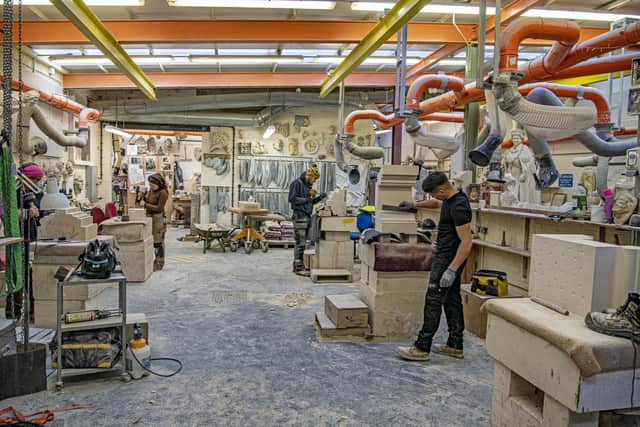

More pertinently, he can see the scaffolding cladding the South Quire. As everyone in York knows, the Minster is rarely free of scaffolding.
Advertisement
Hide AdAdvertisement
Hide Ad“And it never will be,” says McCallion. “After here, we move to the North Quire aisle and when that finishes, we move to the central tower, and that’s a 30-year timetable ahead of us.
“It’s a huge building but it’s a very delicate building and fragile building and needs a lot of work to care for it.”
McCallion is responsible for the Minster estate and the crafts and work needed to maintain the building, including apprentices such as Gee.
“We have six apprentices in the works department,” says McCallion. “It’s not just stonemason apprentices. We’ve got electricians, plumbers, joiners and gardeners as well. It’s the whole spectrum of estate management and heritage crafts that are required to look after this building and the seven-hectare estate.”
Advertisement
Hide AdAdvertisement
Hide AdThe Minster has begun to establish a centre of excellence for heritage craft skills and estate management.
“We’re working with the York Minister Fund to create these new facilities and for our apprentices we will be providing fit-for-purpose accommodation. They will be able to live on site as well as work here, so it’s an incredibly exciting project – a bit like student halls of residence,” says McCallion, adding that the halls will be in what will be called the Heritage Quad behind the Deanery.
The Minster belongs to the Cathedrals’ Workshop Fellowship made up of the nine Anglican cathedrals that still have works departments, and collaborates with cathedrals around the world, including Cologne, Trondheim, Milan and Washington.
“We want to send our apprentices to learn and their apprentices to come to us,” says McCallion. “We’ve had a history of apprenticeships here dating back to the 11th century.”
Advertisement
Hide AdAdvertisement
Hide AdThe Minster’s neighbourhood plan for the precinct will last for 15 years. “It’s all around sustainability, and there are three strands to sustainability,” says McCallion. “Environmental, financial – as it costs £22,000 a day to care for this place – and heritage craft skills, so that we’ve always got people like Charlie and the incredible knowledge capital we have here in the stoneyard passed on to future generations.”
More than 30 people work in the yard. “We have 15 stonemasons, four scaffolders, two plumbers, two electricians, two joiners, four gardeners, heritage builders and then the management team,” adds McCallion.
The South Quire is an 11-year project to restore the stone and place projective glazing in front of the medieval stained-glass windows.
“York Minster has the largest repository of medieval stained-glass windows in the country,” says McCallion.
Advertisement
Hide AdAdvertisement
Hide AdSome of these works of art dating from the 13th and 14th century are still exposed to the elements, and the glass sits in stone that is in a poor state.
It’s a lovely view from McCallion’s office window, but also a reminder of the job that needs doing and will always need doing.
“This is an incredibly special place to so many people, in York, nationally and internationally,” he says.
Later this year, a two-metre-tall statue of the Queen will fill the empty plinth on the Minster’s West Front to mark the 70th anniversary of her accession to the throne.
This has been designed by Richard Bossons, part of the masonry team, and the Queen is waiting in the stoneyard, ready to be elevated.
Comment Guidelines
National World encourages reader discussion on our stories. User feedback, insights and back-and-forth exchanges add a rich layer of context to reporting. Please review our Community Guidelines before commenting.