The story of the Halifax iron foundry that has worked with big names like Sir Antony Gormley
There’s much to admire here such as the beautiful Piece Hall, restored to contemporary elegance, and the Victorian town hall, with its towering spire and startling Charles Barry-designed interiors. Equally, there is beauty in the mundane, in the prosaic things that keep a place going – and flowing.
Tucked down a steep hill, and just past a railway bridge that carries the main Bradford-Manchester line, is Hargreaves Foundry, a firm that has been manufacturing and supplying iron castings in all sorts of shapes and forms since the days of the Victorians. Its website proclaims that “traditional cast iron products are proven to be versatile, durable and reliable”, adding: “These sustainable products continue to meet the changing demands of modern industry.”
Advertisement
Hide AdAdvertisement
Hide AdThey could also add the word “versatile” to that statement, since in recent years Hargreaves has been working closely with the famed sculptor and artist Sir Antony Gormley, advising him on the casting of many of his classic works.
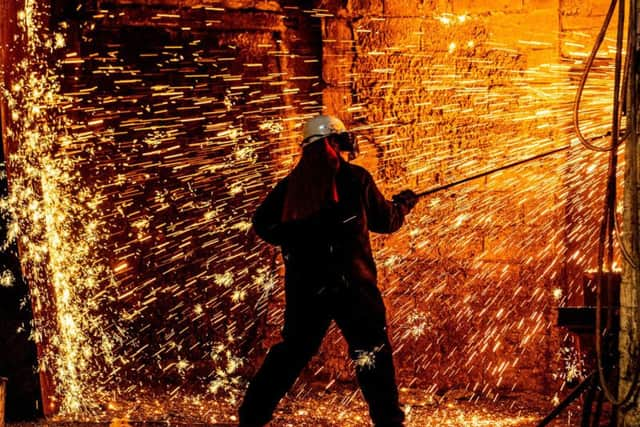

Mick Rath’s trombones are played by some of the best orchestras and brass bands in the world and they are made here in YorkshireYou are, though, as likely to have walked over a Hargreaves Foundry manhole cover as you stroll around the town, as to have driven past the Angel of the North on a jaunt to Tyneside.
At the head of the business, a big employer in Halifax, is Michael Hinchliffe. He is a modern-day successor to the iron masters (or iron founders) of old, but he’s far more concerned today with the advance of modern technology – and keeping up with the latest developments, than he is with what his official title might be.
Halifax-born and raised, Michael began work at the age of 16, as an apprentice pattern-maker, learning a craft that concentrated on templates, wooden patterns and sand-mouldings.
Advertisement
Hide AdAdvertisement
Hide AdIn 1980, there were 3,200 iron foundries across the UK, but now there are less than 50. All have had to diversify to meet changing tastes and demands. Back then, most of the raw products they worked with, the iron and then the steel, came from plants around Britain. These days it is nearly all imported from one place – China.
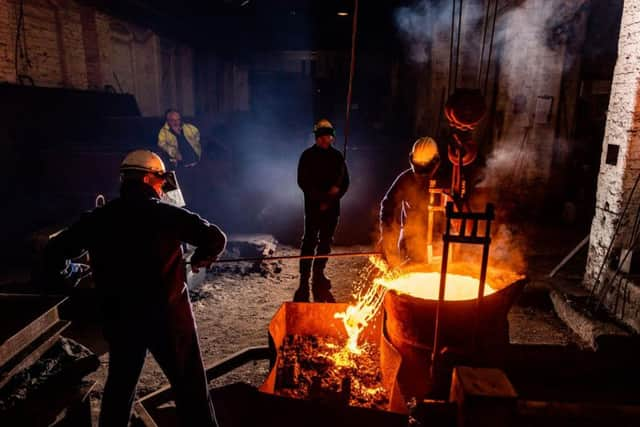

Michael’s vision is a big reason why Hargreaves survived – and now prospers. He realised that it had to move into the “specialised end of the market”. “A good few years back it was very depressing to look around and to examine the market very carefully,” he says.
“What we were doing then meant that we just couldn’t compete on price. We knew that we could do the jobs – but they weren’t wanted any more. We weren’t needed and that was a grim economic reality.”
It prompted some reflection about how the firm could survive. The answer was to make several sidesteps into the art, culture and heritage market. “We did it at just the right time, because there are now so many restoration projects around. We survived while so many other competitors were going bust. And that was very sad. The writing was on the wall for a lot of firms, but instead of ignoring it we read it, learned the lesson and moved on.”
Advertisement
Hide AdAdvertisement
Hide AdThis is where you can walk in the footsteps of Gentleman Jack and see Anne Lister's Halifax todayMichael says Hargreaves is now in a strong position. “Anything the Victorians made in the past, we can make here in Halifax and with new technology it’s much better and more durable. Iron is a fantastic material to work in, and, treated properly and with respect, it will last forever. We can make it, restore it, replicate it – from scratch. Industrial heritage, which is a big part of what we do, isn’t going to go away. There’s a big demand. We are not in decline.”
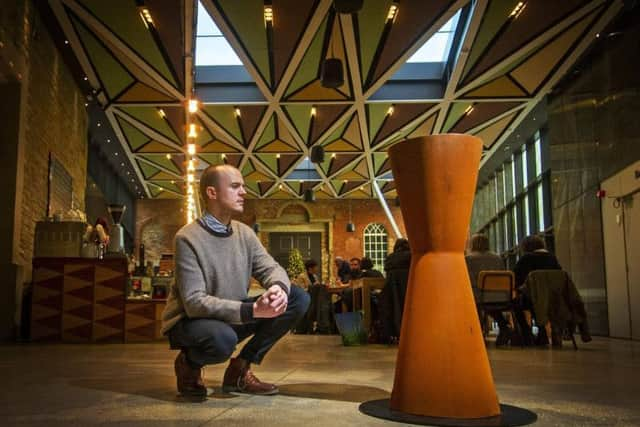

To create the objects that Hargreaves makes on site, there is a regular “big pour” at the Water Lane foundry, in which the molten metal is delivered. Staggeringly, it runs at the rate of five tonnes an hour, with up to 20 tonnes on a single day. Health and safety on site is paramount. “The Victorians took a rather more cavalier approach,” says Michael wryly.
One of Hargreaves’ proudest projects at the moment is the restoration of the Palace of Westminster, and in particular the Queen Elizabeth Tower, the structure that contains Big Ben. The firm is involved right across the board, from restoration of the fancy filigree gargoyles (which you won’t ever see unless you are allowed access to the very highest floors) to the guttering, buttresses and louvres, through to the windows and the cast-iron roof itself.
Who knew that the Victorian architects specified that the tiles should be made of iron, rather than terracotta, and then painted to look like a “natural” roof? Apparently cast iron corrodes much more slowly than steel – that is one of its attractions. “That our work is seen by millions across the world, on a landmark building that is recognised internationally, makes me very proud,” says Michael. “Everyone who looks at a picture of the Houses of Parliament, or who stands outside it, is seeing some of the best that Hargreaves can offer.”
Advertisement
Hide AdAdvertisement
Hide AdHe is fascinated by the history of the firm that he now runs. It was founded in 1881 by Ebenezer Hargreaves, and the family owned it for generations afterwards. In fact, Michael knew the last owner, Kenneth Hargreaves, who was “an extremely honest man – if rather exacting. He was one of those people who believed that ‘if it isn’t perfect, we’re not going to sell it’.”
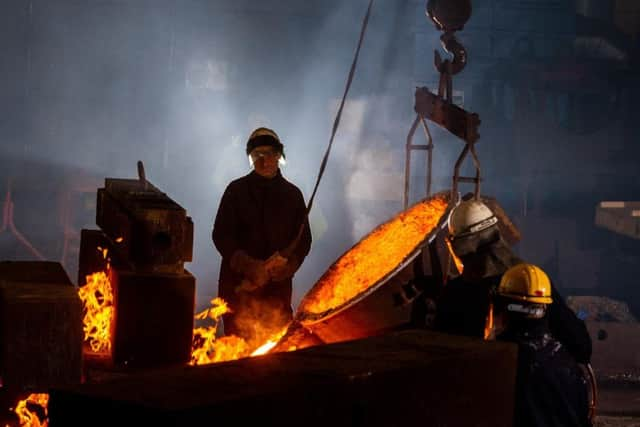

Michael is proud to say he has done every job in the foundry. “So I know what everything requires, and what skills are needed.” He admits to “getting a little thrill when I’m walking around the town, and I see the name of the firm on the ironwork that survives. And I also get a bit annoyed, because so many places have cut corners and taken down the old drainpipes and replaced them with far cheaper plastic. Well, I can tell you right now, that’s a false economy. Plastic will last for a bit and then it will wear, buckle and bend, it’ll have to be replaced. Cast iron was the superior material of Ebenezer’s day, and it remains so in 2020.”
Stage star Barrie Rutter faces cancer fightMichael admits he didn’t know who Antony Gormley was when he first approached Hargreaves (long before he was knighted) to help advise him on his sculptures. “I didn’t know him from Adam but I know that he learned a lot from us. He’s now got his own forge, up in Northumberland, but we are still very much in touch, and we have a close working relationship,” he says.
“We’ve also worked with Anthony Caro [who is well represented at the Yorkshire Sculpture Park]and with many other prominent artists who have seen the beauty in cast iron, and its versatility. It can be so precise and accurate.
Advertisement
Hide AdAdvertisement
Hide Ad“We’re delighted that Sir Antony’s Angel has also gone worldwide. There were just a few smaller versions of it that he sold, all about six feet four inches tall, and now one of them is in the Australian Museum of Art. That’s quite something, isn’t it?
“He’s a visionary, there’s no doubt about that. I’m always interested in how he looks at the world, how he interprets it, and asks questions. He enhances places and locations and, in a lot of ways, our company does that too with the more mundane things around us that we all take for granted.
“We are a niche market, that’s for sure, but it’s such a challenging and enjoyable one, and there’s a ‘knock-on effect’ to the lads on the shop floor. They know that their work and skills are so much appreciated and admired. And to be able to say that, in the world of today, well, that’s something to make you feel pretty good, isn’t it?”