The army of artisan Yorkshire craftsmen shedding new light on Wentworth Woodhouse
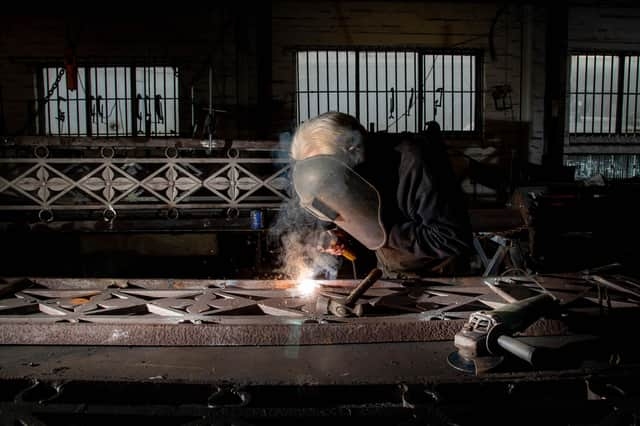

The Earl didn’t stop at the interiors; at great expense, he also lined the mansion’s 606 feet-long facade with six towering, gas-fired lamp standards to add to the sense of grandeur for visitors arriving after dark. The lamp standards were eventually converted to electricity, around 1904 by the 7th Earl, and still stand today. But it’s many decades since they blazed and badly corroded, they were in danger of falling apart.
Wentworth Woodhouse Preservation Trust, which took on the Grade I listed stately home in 2017, has 20 years of restoration and regeneration projects mapped out. Having now repaired a large swathe of the East Front roof and its bookend pavilions, it has turned the spotlight on restoring the lanterns and transforming them to electric. Often, the hardest part of any heritage restoration task is finding a level of craftsmanship and quality materials which match those originally used at the house. Thanks to South Yorkshire’s rich industrial past, however, the Trust didn’t have to look far. Skilled craftsmen who still work to time-honoured traditions have been found - some practically on the doorstep - to carry out the painstaking restoration, which will total £65,000 and, following a public appeal is being funded by The Elizabeth Cayzer Charitable Trust, a private trust which awards grants to organisations in the arts,culture, heritage and science sectors.
Advertisement
Hide AdAdvertisement
Hide AdBlacksmith Andrew Renwick, owner of Ridgeway Forge in Ridgeway and Attercliffe, had the complex task of stripping, repairing and assembling the four-sided fretwork iron standards, which each weigh 600kg and are topped with a 40kg ornamental leaf iron collar supporting a 50kg glass lantern. He’s no stranger to repairing historic ironwork in important settings - the company he took over on the death of his father in 1994 has become one of the country’s most reputable specialists in cast and wrought work, with some of the nation’s best-known stately homes as clients. Andrew and his team - Richard Lewis, James Potterill and Gary Ayres - have worked frequently at Chatsworth House, most notably repairing and conserving the ornate Golden Gates at the Baslow entrance to the estate, which were originally part of a 17th century ironwork screen.
After assessing the lamps’ condition, Andrew’s first challenge was carefully removing the standards without damaging their one-piece, hand-carved stone plinths, and transporting them to his workshop.
“Over the years rainwater had permeated, causing rust-jacking which forces the faces of metal apart. Numerous hasty repairs had been done to prevent them collapsing and bits had fallen off,” says Andrew. “Thankfully, most had been meticulously saved. Working out what went where has been like doing a 3D jigsaw puzzle, but we’ve found that we have 98 per cent of the pieces. Everything has been colour-coded so we know what belongs where.” To strengthen the standards and lengthen their life, each features one new replacement panel.
Hi-tech methods - laser printing and 3D digital modelling - were explored, but the procedure used almost 200 years ago won out. The new sections will be cast from a mould, the pattern for which has been hand-made the traditional way by MD Patterns in neighbouring Elsecar, one of the few pattern-makers still flourishing in the county.
Advertisement
Hide AdAdvertisement
Hide AdJason Dickinson began learning his craft aged 10 in his father Mick’s workshop 42 years ago. Father and son worked together until Mick retired at 74. Some of Jason’s most unusual challenges were the creation of a pattern for a vintage Formula 1 racing car gearbox and the pattern for the Queen Mother’s memorial bronze lanterns lining the Mall on the approach to Buckingham Palace.
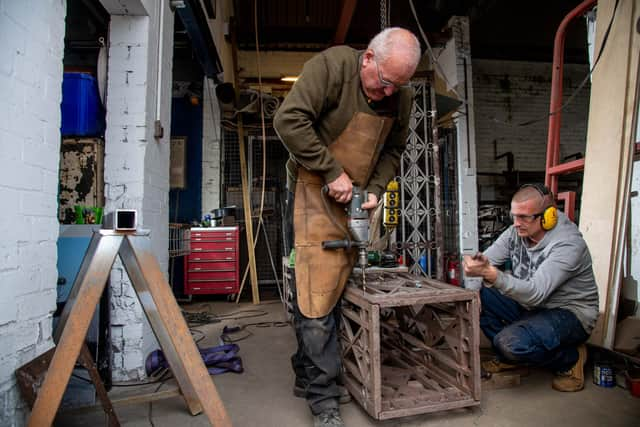

Jason, who first saw Wentworth Woodhouse as an awe-struck seven-year-old on a Brampton Ellis School visit during the mansion’s Lady Mabel College of Physical Education years, was proud to make the pattern for a number of the ornate cast iron gateposts dotted around the house’s grounds some 15 years ago.
One of the original iron lamp standards sides recently arrived at Jason’s workshop on Wilkinson Street, in the heart of the Marquess’s industrial model village, to be remade to exact proportions in wood. Mansfield foundry Trent Castings Ltd, overseen by Clint Murray of Crosslands Foundry in Wincobank, used it to create the moulds in sand, into which molten iron will be poured to create the new structures. “My job is like making a giant model. It involves taking hundreds measurements to ensure everything is spot-on - patterns for engineering work have to be accurate to 10,000th of an inch - and many hours of work with woodworking tools,” says Jason. “It took me 148 hours to create the pattern and though I consider it a work of art, it’s just part of a process. Usually patterns end up gathering cobwebs in a foundry or blacksmith’s store. Sadly sometimes they end up as firewood. It would be nice to think this one could make its way back to the Big House.”
In the meantime, the historic connection between Wentworth Woodhouse and Elsecar is also in play for the restoration of the glass lanterns. They are being restored, reglazed with Georgian-style glass and wired with brass candelabra by Kansa Lighting, whose team of glass artisans and metal workers are based in the Old Flour Mill on Wath Road.
Advertisement
Hide AdAdvertisement
Hide AdAll components will be heading back to Andrew at Ridgeway Forge for assembly beofre being reinstated later this month.
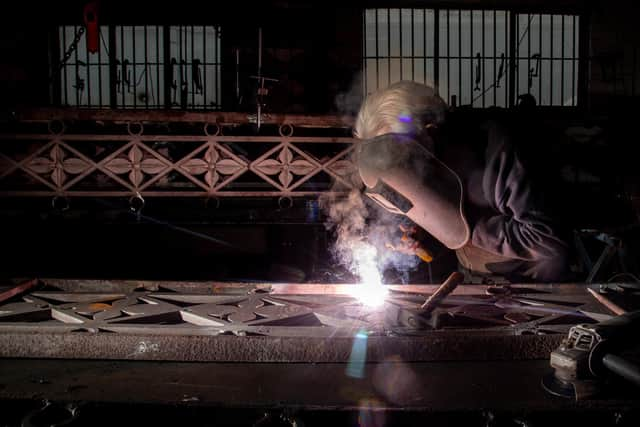

The collars and lanterns will be painted in their original colours by decoration and restoration specialists Hesp Jones & Co of York. The company has restored some of the finest interiors in Britain and Europe, including an 18 month project to restore paintings on the domed ceiling of St Paul’s Cathedral. Its team will also be glazing the iron columns once they are back at Wentworth.
“This is a very challenging but fascinating task. A large team of people with different heritage skills are all intent on restoring what was skilfully made 200 years ago, using exactly the same methods and degrees of care,” adds Andrew. “My team has put in over 1,000 hours. It would have been cheaper and easier to have modern replicas made to replace them. But the level of historic craftsmanship we are discovering at every end and turn is outstanding and simply throwing the originals away would have been a sacrilege. We are all very proud of what we are achieving and are greatly looking forward to seeing the lamp standards illuminating the East Front once again.
“We also hope someone out there might be able to help solve one missing piece in the story of the standards - the original makers left no identifying markings. We feel they could well have been created locally and would love to know by whom.”
Advertisement
Hide AdAdvertisement
Hide AdSarah McLeod, CEO of the Preservation Trust expressed her gratitude to the Elizabeth Cayzer Charitable Trust for funding the entire project and added: “Compared to the major repair programmes at the house, restoring and re-powering the lamp standards may seem a relatively small project But it will make a huge difference to the grandeur of the East Front by night. A range of valuable heritage skills were needed and we were so fortunate to find specialists using these traditional methods close to home.”