Yorkshire joiner Tim invents 'done in a day' homes extensions and loft conversions
Guy Hudson was well aware of the logistical problems in converting the space above his Harrogate town centre shop, which is why he went hunting for a quick and creative solution.
He didn’t have to look far. Richmond-based Moduloft specialises in designing, making and fitting factory-built lofts.
Advertisement
Hide AdAdvertisement
Hide AdInvented by the firm’s owner, Tim Benson, the modular rooms in the roof can be delivered and craned onto site in a day. They come fully fitted with walls, floors, wiring, plumbing and with fitted kitchens and bathrooms, if required.
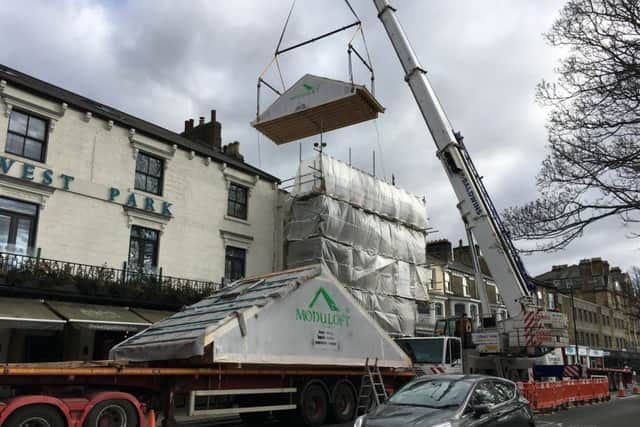

The cost is between 10 and 15 per cent higher than a conventional loft conversion but clients are happy to pay a premium for speed, efficiency and quality.
“It’s a very sensitive site on a high street with a hotel and retail premises adjoining our building so having scaffold up for months while we did a traditional conversion would not have been considerate,” says Guy, who is turning the former Lynx Womenswear building at West Park into a commercial let on the ground floor, with a flat for himself above and a contemporary loft/penthouse apartment for his daughter.
His brief to Moduloft was to build a penthouse with a mezzanine level and a roof-top terrace, while adding walls, floors, fixtures and fittings to provide a living area, a kitchenette, two bedrooms, a bathroom and utility room.
Advertisement
Hide AdAdvertisement
Hide AdIt took six weeks to build in the factory. The existing roof was taken off within a week. As the property is on a main street, a lane closure was agreed with the highways authority, so a crane could park on the road outside the building.
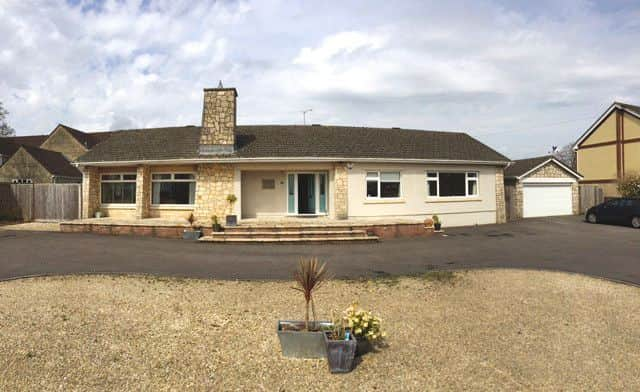

The first module was lifted into place by 7.30am and the remaining three were up by 2pm. The Moduloft team then spent just over a week completing the installation inside ready for Guy to plan the interiors.
He says: “It came ready plumbed and wired with tiles and skylights on the roof and it took an awful lot of stress away from the project. It also allowed us to do it in winter because it wasn’t weather dependent.”
Moduloft is popular with those who want to add value and square footage to bungalows. It has also been a big hit in London, where the speed and efficiency can make all the difference when it comes to planning permission, and in the Channel Islands, where labour is scarce. Recent permitted development rules that make converting offices into homes easier have also brought a demand for ready-made Moduloft penthouses.
Advertisement
Hide AdAdvertisement
Hide Ad“Converting a loft or adding an extra storey in London can add a huge amount of value to a property because prices are so high,” says Tim Benson, a well-known industry innovator.
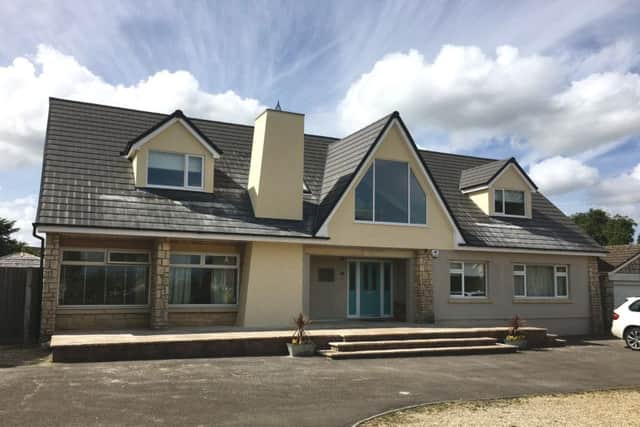

A joiner by trade, he made his name with Trussloft, which he founded 30 years ago. It became the biggest loft converter in the country after Tim devised a system to convert modern trussed rafters to create habitable space.
His ideas were copied, which is why he has patented the designs for Moduloft. He came up with the concept six years ago.
The idea was to reduce work and time on site while cutting the risk factors, such as weather and working at height. The company now installs about 60 Modulofts a year at prices ranging from £60,000 to £500,000. It offers a fully-managed service from design and planning applications to build.
Advertisement
Hide AdAdvertisement
Hide AdTimber is used wherever possible for structural and aesthetic purposes. Tim says: “We do a 3D scan of the building which allows us to design and build the whole thing in sections off-site. That takes about six weeks. Stripping the existing roof usually takes two or three days and lifting the structures on takes a day. It takes another couple of weeks to finish off.
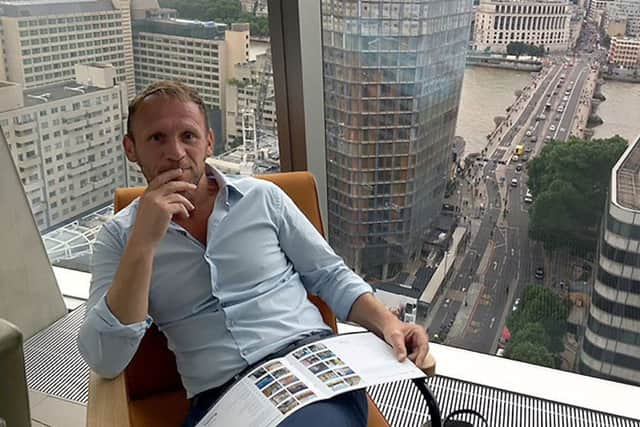

“We’re on site for two or three weeks altogether whereas a traditional contractor would be there for six to nine months.
“People love the speed and convenience and it works very well for properties in inner city or sensitive areas where scaffolding and disruption are an issue.”
Building on his off-site success, Tim has now set-up two more companies: Moduroom, which makes factory-built single and double-height extensions, and Modoroof, a fully tiled, modular roof aimed at developers.
“It’s exciting. For a Moduroom, you need foundations, which takes two days, then you drop the Moduroom on top. The whole extension is ready to move into within a week on site.”