Gripping yarn of mill success
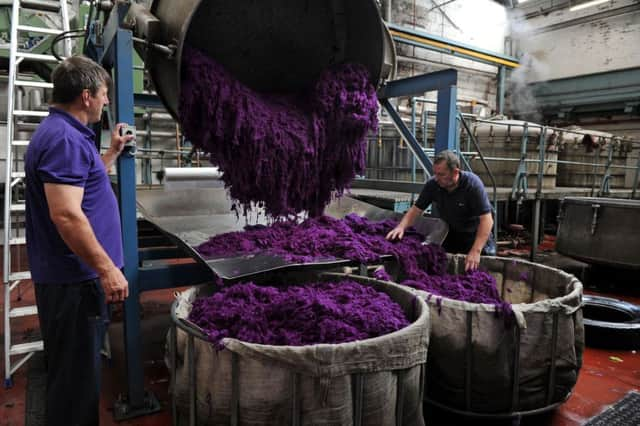

It’s an eye-popping sight followed by the earthy smell of dye, the deafening clatter of looms and, finally, the feel of beautifully soft wool fabric. A tour of Abraham Moon’s mill in Guiseley, near Leeds, is a truly wondrous, sensory experience and one that never fails to impress.
“When we show clients round, their jaws drop. They just don’t realise the amount of work that goes into making a piece of cloth,” says Michele Jones, marketing manager of the last remaining vertical mill in England.
Advertisement
Hide AdAdvertisement
Hide AdMoon’s customers include Burberry, Ralph Lauren and Dolce and Gabbana, along with John Lewis, Barbour and Boden. Its interiors fabrics and throws are in the White House, stately homes and castles and they retail in Harrods and at Highgrove.
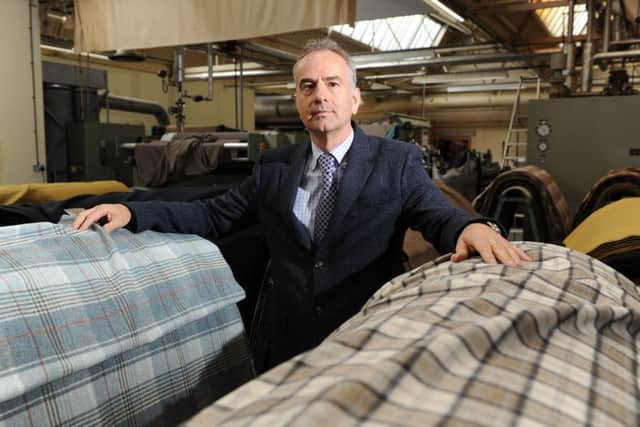

But while the firm’s heritage and manufacturing processes are appealing, what the designers and buyers care most about is the quality and that’s what a well-run vertical mill can deliver, because everything, apart from the sheep shearing, is done in-house.
The wool is imported from South Africa and New Zealand because their fleeces are softer and most suitable for fabric, while the coarse wool from British sheep is best for carpets.
But the magic that turns fleece to cloth is all done in this Yorkshire factory, from scouring and combing to dyeing and blending the fibres, then spinning, winding and weaving, and, finally, laundering the fabric in gigantic washing machines using the purest water from an 800ft bore hole.
Advertisement
Hide AdAdvertisement
Hide AdQuality control is strict and there’s a lab. where material is tested for durability and shrinkage. Another selling point is the number of different coloured yarns blended together to make one fabric.


“This is where we beat the overseas competition. They will use one colour and that can look quite flat. Whereas, if you take our grey cloth and look closely it has bits of yellow, blue and black in it too. It’s more complicated to make but it gives it depth and richness,” says Michele, who adds that another advantage of having everything under one roof is the ability to respond quickly to last-minute requests.
It has all helped Moon’s become a national treasure, a reminder of our great textile heritage and a remarkable lesson in survival.
After making vast sums of money in their Victorian heyday, most of Britain’s textile mills declined and eventually went to the wall. Some were mismanaged and milked by profligate sons, others swamped by too many shareholders. Most were massacred by foreign competition.
Advertisement
Hide AdAdvertisement
Hide Ad“Towards the end of the 1980s, demand for wool fabric was declining and producers from Italy, Spain, Portugal and Eastern Europe were selling it more cheaply than us. Then in the 1990s, China started exporting it. They were the toughest years by far,” says Moon’s MD and chairman John Walsh, who has led the 177-year-old business into the 21st century.
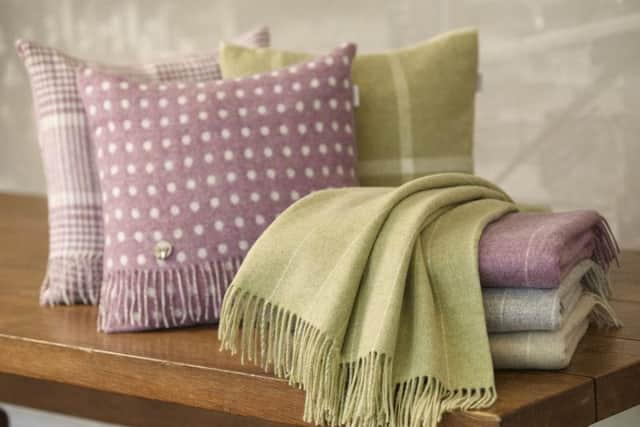

John’s decision to go upmarket rather trying to compete with bargain basement prices is what saved the factory. It was risky but it worked, fuelled by a belief that Yorkshire’s finest could beat anything else out there.
“It was pointless to try and compete with other producers on price. Their wage bills were low and the Chinese government subsidised the industry. The idea, of course, was to kill off the competition and it worked.
“We focused on quality, design and bespoke products. Interestingly, a lot of retailers who took their business to China have come back because we can give them better quality and service.
Advertisement
Hide AdAdvertisement
Hide Ad“The price differential has also eroded. It’s only about 25 per cent,” says John, whose great-grandfather bought the company in 1920 and continued the work of Moon dynasty.
The stability and continual investment by the two families has benefited the company, which was started in 1837 by Abraham Moon.
“We have always reinvested the profits in new technology. A lot of other mills were like museums because they had stopped investing. They wrote their own death warrant,” says John.
The looms, which can produce 30,000 metres of cloth a week, are now controlled by just a handful of people.
Advertisement
Hide AdAdvertisement
Hide AdSome things, however, remain the same, like the Wakes weeks, when the mill shuts down for most of August and the ghosts of the past come back to play.
“It can feel very eerie and I’m not keen on walking through on my own,” says Michele, who has a swanky new office thanks to recent expansion that gives the company 300,000 sq ft of space.
It was a big investment helped by the recent diversification into interiors fabrics and Bronte by Moon throws, blankets, cushions and scarves, which now represent half the business.
Sales are soaring, especially in Japan, America and Northern Europe, prompting the firm’s first venture into retail with the first Moon first shop at The Courtyard just outside Settle.
Advertisement
Hide AdAdvertisement
Hide AdThe future looks good, though the firm still struggles to attract apprentices. The bright young things think that mills are dark, satanic and so last century.
“They don’t realise that textiles isn’t just a job,” says John Walsh.
“It offers a career and opportunities that are far more interesting than most industries.”
• www.moons.co.uk; The Courtyard, Settle, www.inthecourtyard.co.uk