Sneak peak at the mail model in Amazon’s mega-store
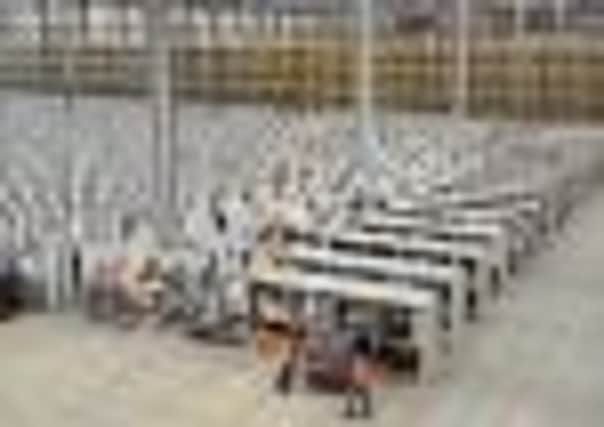

At reception, all is calm as people sign in and out, but security is tight, because through the set of double doors beyond lies a space the size of six football pitches stacked with consumer goods worth millions of pounds.
From tools to toys and TVs to tyres, this is where orders are picked out minutes after customers hit the “buy” button on Amazon, which, in the jargon, is among the world’s biggest internet shopping “platforms”.
Advertisement
Hide AdAdvertisement
Hide AdIn fact, the variety of jargon and acronyms used here is almost as dazzling as the array of products, with the company’s “fulfilment centre” giving its “associates” written instructions at every turn.
Amazon is reluctant to say exactly how many staff work at its centre in Balby, Doncaster, saying only “hundreds” and that’s probably because many of them are on temporary contracts, brought in when needed.
But in the run-up to Christmas, the company is keen to talk about the extra staff it is taking on, both here and at its seven other warehouses, which deal with many millions of items a week.
Certainly nothing appears in short supply, as pallets packed with pushchairs and carts containing computer equipment are towed in and out by electric vehicles.
Advertisement
Hide AdAdvertisement
Hide AdAs they arrive on lorries, the so-called “perfect pallets” which contain several of the same item are examined for damage before being taken away and stored in huge racks standing 50ft high.
Pallets containing a mixture of goods are taken apart by a team of “receivers” who check each item for damage before it is given a barcode and stored in what the company calls its “random stowage” area.
Presiding over the whole operation is Nicola Sweeney, who started her Amazon career as a stock analyst, but moved through the ranks almost as quickly as one of the firm’s parcels hits the road.
Casting aside the jargon for her title, the 34-year-old introduces herself as the centre’s general manager and as she leads a tour of the miles and miles of aisles, it’s clear she enjoys the buzz.
Advertisement
Hide AdAdvertisement
Hide AdGrabbing one of the hundreds of barcode readers issued to the warehouse “pickers”, she says: “I’ve had jobs where I have gone home at night and thought: ‘What have I achieved today?’
“Here it’s different, to see the orders coming in and to know that by the end of the day we have sent thousands and thousands of items out to people who are waiting for them feels great.”
In this warehouse, there is no sign of the books that first made Amazon famous – they are dealt with at one of the other centres.
Here it’s mainly about the bigger items the website sells.
Among the random stowage shelves there is a baby seat for a bike stacked next to rubbish bins alongside Lego and several DVD players.
Advertisement
Hide AdAdvertisement
Hide AdBut the computer and its barcode system pinpoints every item, every time.
Once a picker has completed their “route” it is over to the packing area, where rows and rows of “packers” stand putting each item into the familiar brown Amazon box.
The boxes are then placed onto a conveyor next to them and travel to an operator manning a weighing scale, which is not to work out how much the parcel will cost to post, but to ensure the item inside is correct.
Ms Sweeney says: “The computer knows the weight of the item, and the weight of the box. If the weight is wrong the package doesn’t go out.”
Advertisement
Hide AdAdvertisement
Hide AdIt is only at this stage that the final address label is printed and the parcel goes into a trolley which is then loaded onto a lorry.
And as soon as the truck leaves with a parcel on board, Ms Sweeney says, the computer knows that an order is on the way, and it sends out an email to customers to say so.
She adds: “From the moment the order is placed to the second the item leaves the warehouse can be just a few hours.
“That’s always our aim.”